How to Choose the Right Planetary Mixer for Your Business Needs
Planetary Mixer Manufacturer
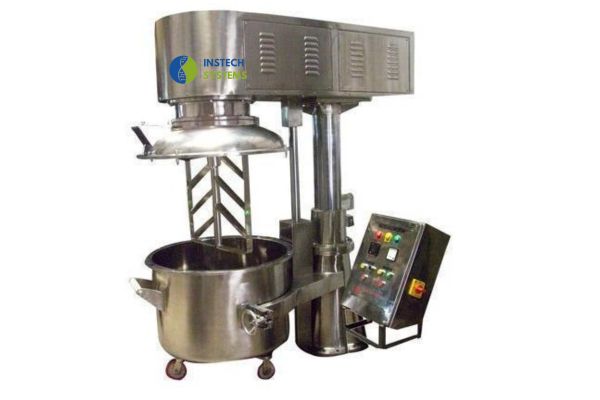
Choosing the right planetary mixer for pharmaceutical applications requires a careful evaluation of several factors to ensure it meets the industry’s stringent quality and performance standards.
1. Capacity and Batch Size Requirements
- Evaluate the scale of your production: consider the size and volume of batches the mixer needs to handle.
- Choose a mixer that can accommodate current production needs and has some flexibility for future expansion. Planetary mixers come in various capacities, from laboratory scale (5–20 liters) to full production scale (up to 1000 liters or more).
2. Material Compatibility
- Select materials that ensure compatibility with pharmaceutical-grade substances and meet regulatory standards.
- Stainless steel (SS316) is typically preferred for its resistance to corrosion, ease of cleaning, and compatibility with pharmaceuticals.
- Some planetary mixers also offer coatings or linings to prevent contamination or reaction with ingredients.
3. Mixing Mechanism and Speed Variability
- Ensure the planetary mixer offers variable speed control and multiple mixing speeds, which are essential to achieve different textures and consistencies required for pharmaceuticals.
- Check that the mixer is capable of precise control over mixing speeds and torque. This control helps prevent the degradation of sensitive ingredients and allows for the consistent mixing of active pharmaceutical ingredients (APIs).
4. Vacuum and Pressure Capabilities
- Many pharmaceutical applications require mixing under a vacuum to remove air pockets and avoid oxidation. If your formulation requires this, look for mixers with a vacuum-sealing option.
- Some planetary mixers also support pressure mixing, which can be useful for certain pharmaceutical formulations to ensure homogeneity and stability.
5. Temperature Control and Heating/Cooling Options
- Temperature control is essential in the pharmaceutical industry, as certain drugs or formulations require mixing at specific temperatures to maintain stability.
- Choose a planetary mixer with integrated heating/cooling jackets to enable precise temperature control during mixing.
6. Cleanability and Compliance with cGMP Standards
- Look for a mixer that complies with current Good Manufacturing Practices (cGMP). It should be easy to disassemble and clean, with minimal crevices or surfaces where contaminants could accumulate.
- CIP (Clean-in-Place) and SIP (Sterilize-in-Place) options are advantageous for maintaining hygiene standards, minimizing downtime for cleaning, and reducing the risk of cross-contamination.
7. Automation and Programmability
- Automated planetary mixers with programmable control panels allow for more consistency in production by storing multiple recipes and operating sequences.
- Programmable logic controllers (PLCs) and human-machine interfaces (HMIs) can be integrated to simplify batch processing and ensure repeatability, which is especially crucial in pharmaceuticals for regulatory compliance.
8. Safety Features
- Ensure the mixer includes safety interlocks, emergency stop functions, and other safety features to protect operators.
- Rigid safety standards are mandatory in the pharmaceutical industry, and mixers with reliable safety mechanisms can help avoid accidental exposure to hazardous materials.
9. Energy Efficiency and Durability
- Look for mixers that optimize energy usage without compromising on performance. Energy-efficient models reduce operational costs and support sustainable practices.
- Choose a machine known for durability, especially if you anticipate long operational hours, as downtime for repairs can disrupt pharmaceutical production schedules.
10. Cost and Manufacturer Support
- Evaluate the total cost of ownership, including initial purchase price, maintenance, and potential downtime costs.
- Reliable after-sales support and access to spare parts are essential for minimizing disruptions, so it’s important to choose a reputable manufacturer with a track record of excellent support.
Conclusion
Choosing a planetary mixer for the pharmaceutical industry is not just about capacity but involves evaluating the machine’s compliance with industry standards, flexibility in batch size, control over mixing conditions, ease of cleaning, and safety features. An investment in a high-quality mixer designed specifically for pharmaceutical applications can significantly enhance the efficiency, safety, and quality of your production process.
Summary
To choose the right planetary mixer, assess your production volume, mixing requirements, and available space. Look for durability, the necessary capacity, speed options, and safety features to ensure that your investment meets the demands of your business. Planetary mixer machine used in the pharma industry.